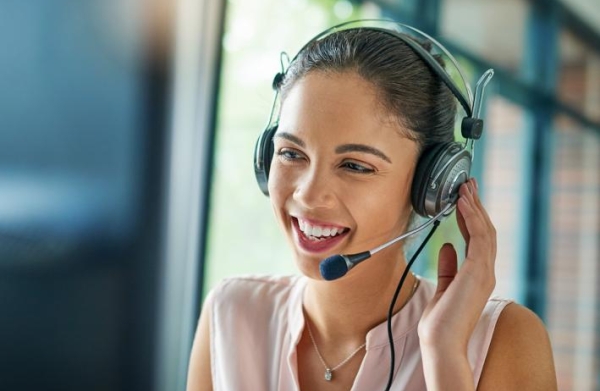
How we can help
The main software package we use is COMSOL Multiphysics®. This software package is based on the finite element method, which is a flexible technique that can be used to model complex geometries and a range of different physics. Our extensive experience with COMSOL and its wide range of functionality allow for fast development of detailed simulation models.
By using realistic simulations in 1D, 2D, 2D axisymmetry, or 3D, we can optimise existing products and design new products more quickly. Simulations also help our designers, researchers, and engineers to gain insight into problems that are difficult to handle experimentally. By testing a design before manufacturing it, we can save companies both time and money.